How to Choose the Perfect Insulation Material for Cold Storage
Date:2024-03-28
With the advancement of industries and the improvement of living standards, preservation and freezing have become vital aspects of the consumer market. Cold room panels, as integral components of cold storage construction, play a critical role in the daily operations of such facilities. Cold storage facilities demand high standards for air temperature, humidity, and environmental conditions. Therefore, selecting the appropriate panel type is crucial, not only for maintaining the cold storage effectively but also for saving energy and reducing costs.
The choice of insulation material greatly influences the energy efficiency and operational costs of cold storage. Here are some commonly used insulation materials for cold rooms:
Polyurethane (PIR): Polyurethane is a widely employed insulation material for cold storage, renowned for its outstanding insulation performance and mechanical strength. It effectively prevents heat transfer and minimizes heat loss. Moreover, polyurethane insulation materials possess moisture resistance, waterproofing properties, and corrosion resistance, making them suitable for various cold storage environments.
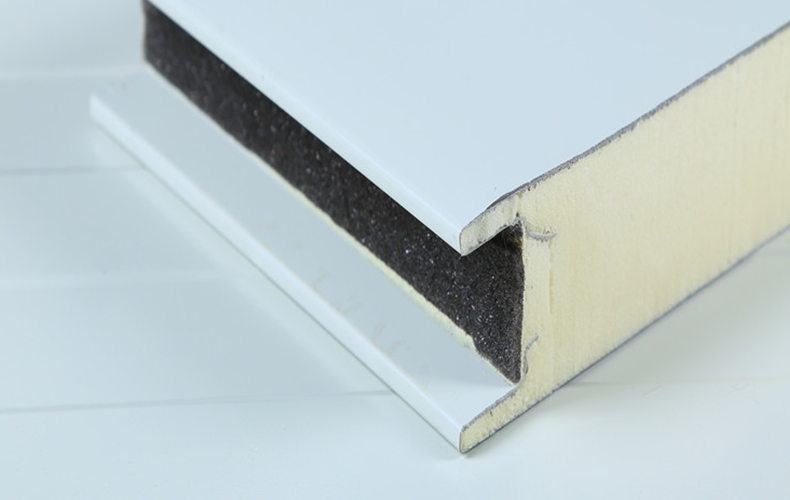
Extruded Polystyrene (XPS): XPS is a high-performance insulation material with low thermal conductivity and excellent compressive strength. It is commonly employed in cold storage facilities with stringent insulation requirements.
Rockwool: Rockwool is a fibrous material made from melted rocks, offering excellent insulation and sound absorption properties, as well as remarkable fire resistance. However, it is relatively expensive, and protective measures must be taken during construction.
Among these options, polyurethane stands out in the cold storage industry due to its exceptional insulation performance, moisture resistance, waterproofing capabilities, superior fire resistance, and ease of installation. It is the ideal choice for cold storage insulation, ensuring safe and efficient operations while meeting environmental requirements.
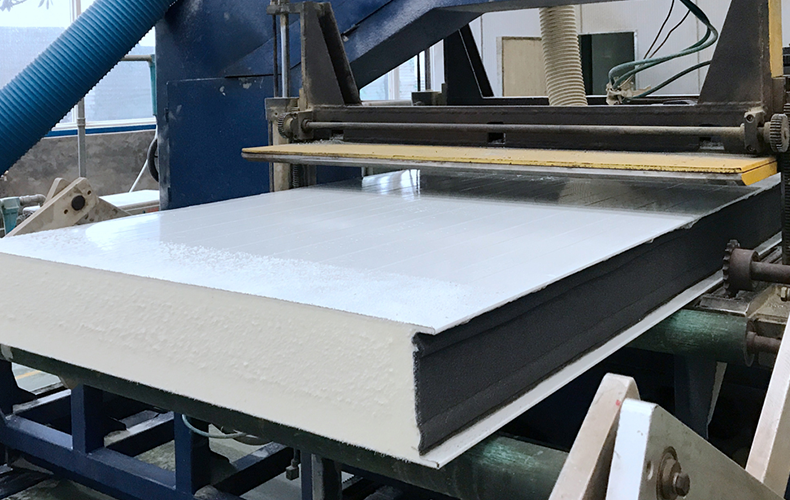
BRD Cold Room Panels, jointly developed by BRD group and international chemical company BASF, utilize BASF's rigid foam material produced through pentane foaming. These panels meet the B1 level requirements for flame retardancy, catering to the market's demand for highly flame-retardant products. Moreover, BRD Cold Room Panels exhibit lower thermal conductivity compared to traditional insulation materials, resulting in a 20% improvement in thermal insulation performance. They are the optimal choice for constructing various types of cold storage projects, contributing to a more energy-efficient and sustainable future.
Need expert advice or a quote? Reach out to us today!
WhatsApp: +86 18638188782
Mobile: +8618638188782
Email: marketing@brdecogroup.com
The choice of insulation material greatly influences the energy efficiency and operational costs of cold storage. Here are some commonly used insulation materials for cold rooms:
Polyurethane (PIR): Polyurethane is a widely employed insulation material for cold storage, renowned for its outstanding insulation performance and mechanical strength. It effectively prevents heat transfer and minimizes heat loss. Moreover, polyurethane insulation materials possess moisture resistance, waterproofing properties, and corrosion resistance, making them suitable for various cold storage environments.
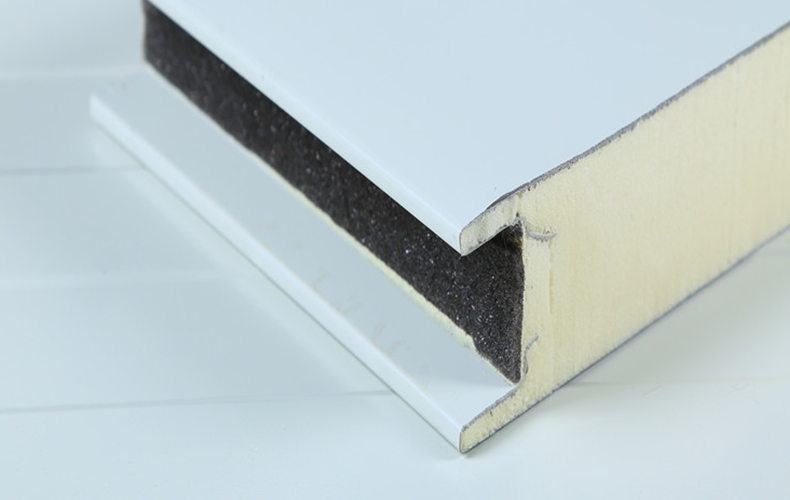
Extruded Polystyrene (XPS): XPS is a high-performance insulation material with low thermal conductivity and excellent compressive strength. It is commonly employed in cold storage facilities with stringent insulation requirements.
Rockwool: Rockwool is a fibrous material made from melted rocks, offering excellent insulation and sound absorption properties, as well as remarkable fire resistance. However, it is relatively expensive, and protective measures must be taken during construction.
Among these options, polyurethane stands out in the cold storage industry due to its exceptional insulation performance, moisture resistance, waterproofing capabilities, superior fire resistance, and ease of installation. It is the ideal choice for cold storage insulation, ensuring safe and efficient operations while meeting environmental requirements.
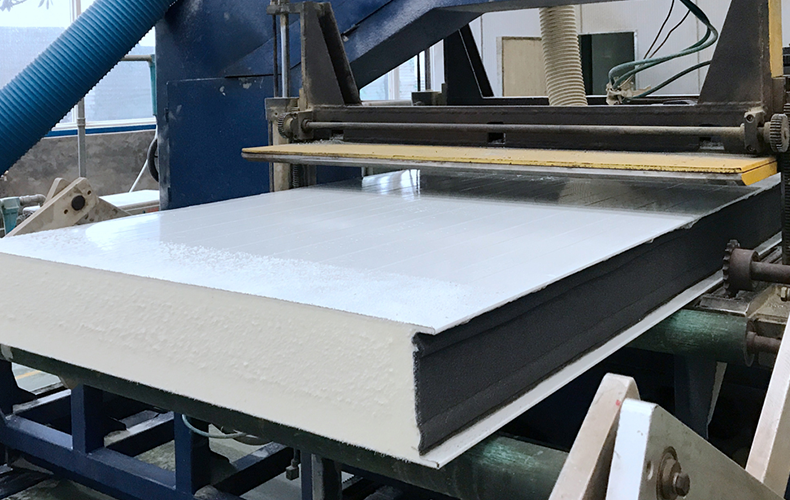
BRD Cold Room Panels, jointly developed by BRD group and international chemical company BASF, utilize BASF's rigid foam material produced through pentane foaming. These panels meet the B1 level requirements for flame retardancy, catering to the market's demand for highly flame-retardant products. Moreover, BRD Cold Room Panels exhibit lower thermal conductivity compared to traditional insulation materials, resulting in a 20% improvement in thermal insulation performance. They are the optimal choice for constructing various types of cold storage projects, contributing to a more energy-efficient and sustainable future.
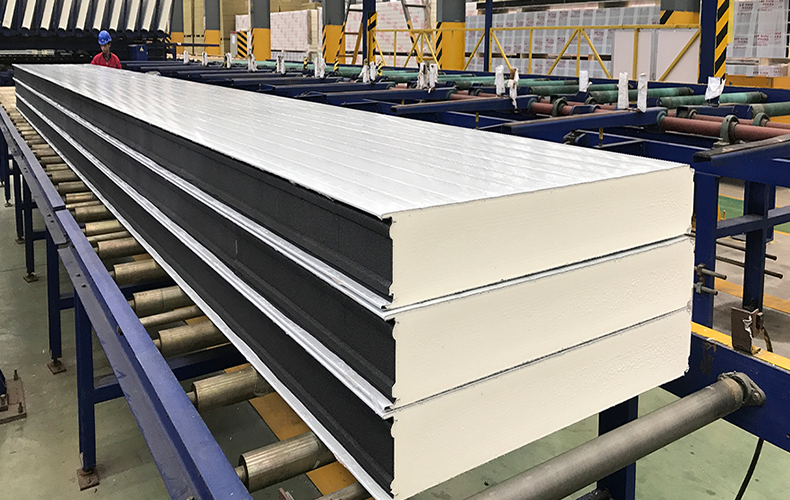
Need expert advice or a quote? Reach out to us today!
WhatsApp: +86 18638188782
Mobile: +8618638188782
Email: marketing@brdecogroup.com
Back to List
Latest News
-
2025-04-19BRD Plays Key Role in Ant Medical Malaysia's New State-of-the-Art Facility
-
2025-04-03BRD Expands Presence in Saudi Arabia with Upcoming Exhibition
-
2025-03-20Embracing Spring, Ushering in a New Era
-
2025-03-14Innovation in Focus: BRD Showcases Advanced Panels at WORLDBEX 2025
-
2025-03-10BRD's Innovative Curved Corner Sandwich Panels